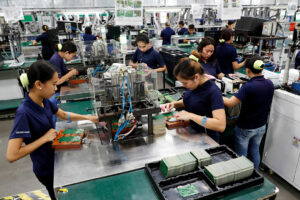
Growing the electronics industry
Visiting US Commerce Secretary Gina Raimondo told a press conference on Monday that US investors were looking at the Philippine semiconductor industry with the target of increasing the number of packaging, testing, and assembly facilities in the country. This is to primarily diversify the US chip supply chain, which she said was too concentrated in a few countries.
Given the Philippines’ proximity to Taiwan, which is a major chip producer, I guess it does make sense for the US to look just a little down south. After all, Taiwan and the Philippines use the same shipping lanes to the West. Ditto for major chip makers South Korea and China. We are all in the same general area of the globe, including Japan, which is reviving its chip-making industry.
And it may be easier for foreign manufacturers now operating in China to relocate to other production hubs in the region, rather than having to go back to their home countries. Taiwan and the Philippines are the options, and perhaps even Vietnam. Japan, in fact, is bent on boosting its chip-making industry ASAP by putting more resources in Japan and in Taiwan operations.
One cannot help but think that present developments in the semiconductor industry are all connected to geopolitics, as a way of limiting the world’s electronic chip dependence on China. Foreign companies now manufacturing in China can move production bases back “home” or to economic allies in the Asian region.
The US Commerce Department has imposed new restriction on exports to China of semiconductors and other technology products amid political tensions. And now, the US government is also offering tax breaks and perks to US electronic companies to move out of China and go to ally countries. Japan has also restrictions on the sale to China of chip-making equipment.
These are unsurprising moves for Japan and the US, which suffered chip shortages because of supply chain issues during the COVID pandemic from 2020 to 2022 and then after. Note that the US, Japan, and Korea are all major automotive manufacturers, and the car industry was among those adversely affected by chip shortages.
And with the electric vehicle industry growing globally, batteries, electronic chips, wiring harnesses, and electronic components are now in even greater demand worldwide. The race is on in securing minerals and other raw materials as well as supplies needed in electronics production. Speed to market requires the proximity of resources to production hubs and customers.
Going back to the US looking at the Philippines, recall that electronics companies Analog Devices, Amkor Technologies, and Texas Instruments, among others, have been operating in the country since the 1970s. Intel also has a plant in the Philippines. And Motorola was here for some time. In short, the US electronics industry has been producing here for the last 50 years.
To date, the Philippines reportedly has 13 semiconductor assembly, testing, and packaging facilities. And then there are numerous electronic manufacturing service providers and assemblers. Wiring harness companies operate here as well, and car components makers as well as producers of consumer durables.
Ms. Raimondo points to the Philippine advantages: talent, expertise, democracy, rule of law, transparency, anti-corruption, and reasonable regulations; in what seemed to be a dig at China. But, of course, this is not to mention the US attempt to strengthen relations with the Philippines to mitigate our stronger pivot to China as a political and economic partner.
Department of Trade and Industry (DTI) Undersecretary and Board of Investments Managing Head Ceferino S. Rodolfo noted that this US initiative was anchored on local “talent development,” and thus the need for “skilling and upskilling” the local talent pool. The US is said to be offering over $50 billion in subsidies to chip makers operating in China to relocate back to the US or its allies.
But American Chamber of Commerce of the Philippines Executive Director Ebb Hinchliffe said the cost of power in the Philippines is the major challenge. “The biggest obstacle is the cost of energy and consistent power. You can’t have a wafer factory or a semiconductor factory to go on and off, because that could cost you a million dollars,” Mr. Hinchliffe said.
Considering the developments in technology now, one industry insider told me that other than the cost of power, the other challenges moving forward are cost of financing and cost of logistics. He mentioned the transition away from the labor arbitrage model, where competitiveness is derived from lower cost of labor in production, because of automation and artificial intelligence.
Simply put, particularly in electronics manufacturing and semiconductors, business owners are bound to invest more in “smart” factories that can efficiently run with fewer workers. This, in a way, will shift labor cost away from factory workers to factory managers, and will push more investments into robotics, automation, and operations with limited human intervention.
Obviously, this transition to new technology will require a big amount of capital, which can drive up the cost of financing. High-technology manufacturing, with automation and artificial intelligence, will also push up the electricity requirement of operations. Then, higher manufacturing efficiency can lead to faster turnaround times and greater demand for logistics.
As technology costs come down, and labor costs drop, cost of energy, financing, and logistics will become more important considerations, and will greatly influence competitive advantage. Manufacturing will more likely gravitate closer to what the insider referred to as points of consumption where logistics, cost of money, and energy costs will also be lower.
He also noted the need to boost the local design talent pool, noting that originality in design and product or process uniqueness would become more important considerations in the future. Thus, there is even greater need to develop downstream industries, with Philippine-designed electronic products making use of locally made chips and locally assembled components.
The greater challenge, I believe, is whether the government, through its policies, can help local manufacturers take advantage of emerging opportunities in the electronics industry. Success cannot rely solely on the private sector. There should be a concerted effort, a stronger public-private partnership, to bring the Philippines to the 22nd Century.
Marvin Tort is a former managing editor of BusinessWorld, and a former chairman of the Philippine Press Council.